[Beckhoff 어플리케이션] XTS를 통한 효율적인 플라즈마 분리 카드(PSC) 생산으로 HIV 테스트에 대한 접근을 간소화
Roche: 플라즈마 분리 카드의 비용 효율적이고 유연한 생산
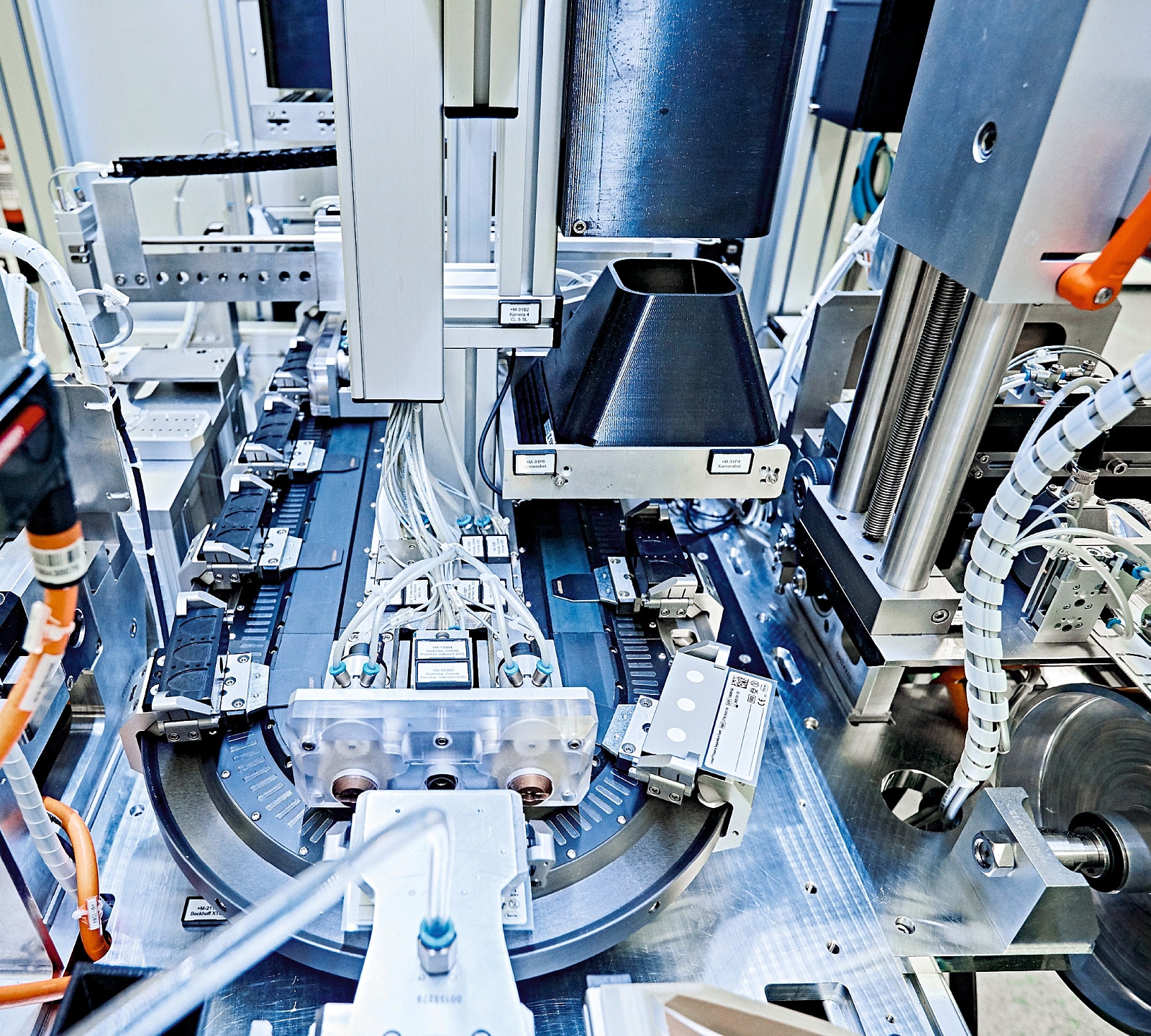
10 개의 무버와 3m의 트랙을 가진 XTS는 플라즈마 분리 카드 생산 장치의 중심 요소 역할을 한다.
Roche는 원거리 지역의 HIV 환자를 검사하고 모니터링 하는 것을 개선 및 간소화시킨 새로운 기술 Cobas 플라즈마 분리 카드를 개발했다. 처음으로, 혈장 샘플을 실험실로 운반하는 동안 냉각시킬 필요가 없게 되었다. 이 혁신적인 기술의 전제 조건에는 플라즈마 분리 카드를 비용 효율적으로 생산할 수 있게 하는 유연하고 콤팩트한 역동적인 생산 기술이 있어야 한다. 이는 Beckhoff의 XTS (eXtended Transport System)를 통해 실현되었으며, 높은 유연성으로 효율성을 증가시켰다.
스위스 바젤에 본사를 둔 Roche 그룹은 100여 개의 국가에서 활동하고 있으며 전 세계적으로 약 94,000명의 직원을 고용하고 있다. 이 회사는 주로 제약과 진단 사업을 병행하며 개인 맞춤형 의학의 선두주자 중 한 업체로서 지금의 위치에 있다. 진단에서 제약 제품에 이르기까지 전체 가치 창출 사슬은 혁신의 큰 잠재력을 제공한다. 약 8,300명의 직원이 근무하는 독일 만하임의 Roche가 대표적 사례이다. Cobas 제품군의 일부인 새로운 플라즈마 분리 카드는 적절한 HIV 치료법을 결정하기 위한 세계 보건기구의 민감도 요구 사항을 충족한다. 이 신제품은 후속 HIV 바이러스 부하 테스트를 위한 안정적이고 사용하기 쉬운 혈장 샘플링 카드이다.
대략 신용 카드 정도 크기의 Cobas 플라즈마 분리 카드는 환자의 손가락 끝에서 나온 적은 양의 혈액만 필요로 하며, 혈장 샘플 운반도 크게 단순화시켰다. 예를 들어 사하라 이남 아프리카 시골 지역 사람들의 경우, 실험실로 이동하는 동안 혈액 샘플을 냉각시킬 필요가 없기 때문에 HIV 검사에 더 쉽게 접근할 수 있다. 이와 같이, 플라즈마 분리 카드는 혈장 샘플을 채취하고 준비하는 방법을 크게 변화시키고, 극심한 열과 습도가 있는 환경에서도 신뢰할 수 있는 정량 테스트를 용이하게 한다.
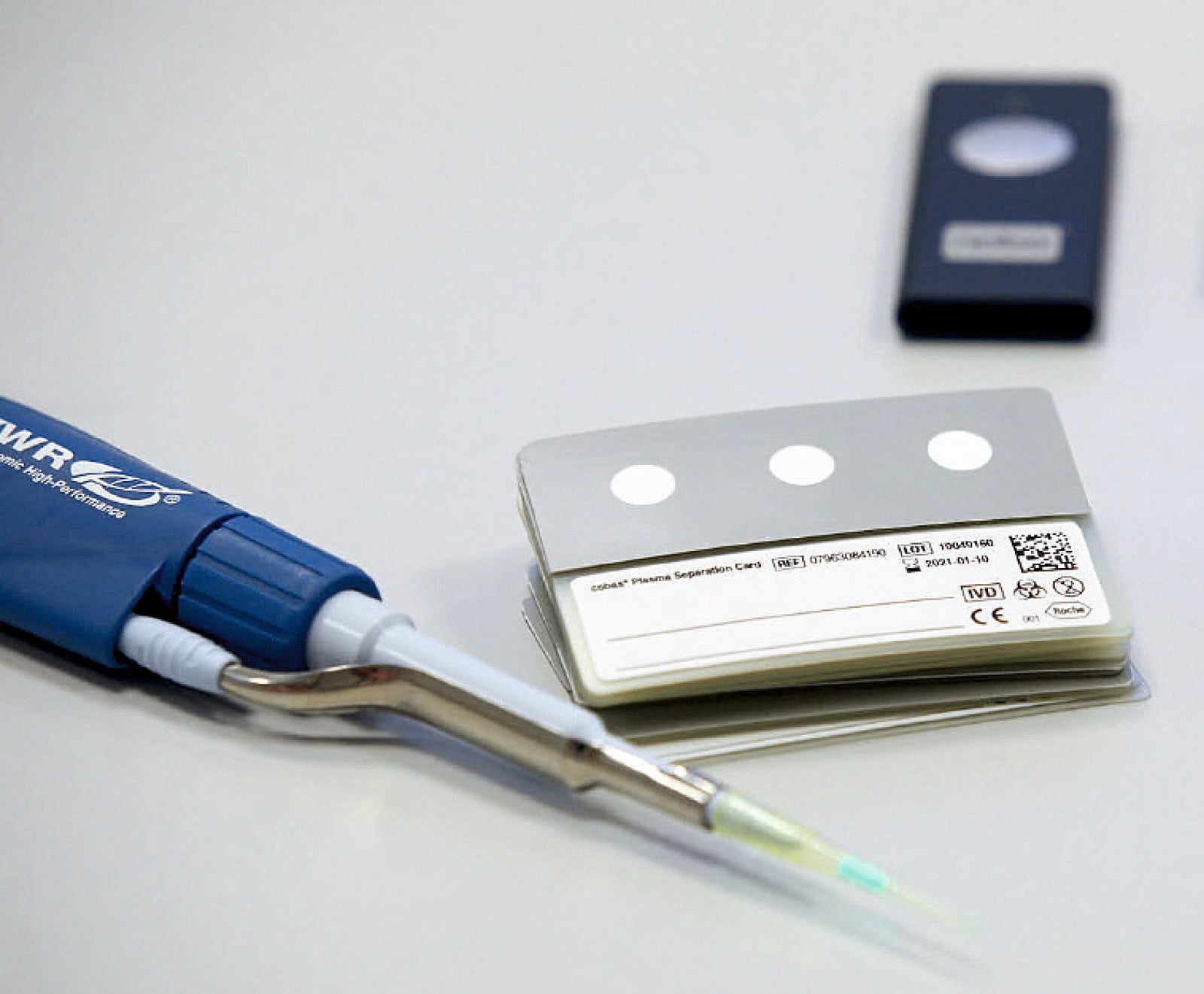
Cobas 플라즈마 분리 카드는 접착 부직포가 있는 캐리어 층과 보호 및 라벨링을 위한 상부 층으로 구성된다.
복합 카드 출시기간 단축
플라즈마 분리 카드는 약 3.5 x 3 m 크기의 소형 기계로 제조되며, 여기서 Beckhoff의 XTS가 중심적인 역할을 한다. 플라즈마 분리 카드는 독일 만하임에 있는 Roche의 제조 서비스 및 기술 부서의 기계 공학 전문가들에 의해 개발되었다. Roche의 전문 엔지니어인 Lukas Nagel은 개발 및 생산 부서의 전문가들이 서로 협력하여, 제품생산 준비까지 이 프로젝트를 2년 안에 완료할 수 있었다고 설명한다. XTS는 개발 과정에서 변경해야 하는 요구사항에 맞춰 생산 단위를 조정할 수 있었기 때문에 매우 유연한 이송 시스템으로서 중요한 역할을 한다. XTS는 소프트웨어 기반 기능을 사용하여 프로세스를 최적화하여 신속하게 구현할 수 있으며, 이를 수정하기도 쉽다.
XTS는 여러 층으로 구성된 플라즈마 분리 카드의 복잡한 구조를 고려할 때 중요하게 여겨졌다고 Lukas Nagel은 설명한다. 캐리어 층은 기계 고정용으로 사용된다. 그 다음 얇은 접착층이 혈장 분리막에 부착된다. 그 아래에는 화학적 안정제로 분리된 부직포 물질이 있어 운반 중 최대 6주 동안 사람의 혈장을 보존할 수 있게 한다. 그리고 환자의 정보를 손으로 기록할 수 있는 라벨이 제공된다. 마지막에는 보호층이 있다. 이 제품의 혁신적인 특징은 안전한 이송을 위해 사람의 혈장을 약간만 건조하면 되고, 실험실에 도착된 후에 샘플을 쉽게 액화하여 일반 혈장과 같은 방식으로 분석할 수 있다는 점이다.
플라즈마 분리 카드의 복잡한 구조는 정교한 생산 공정에 의해 설명된다. 캐리어 층은 주로 샘플 이송에 사용된다. 두 개의 접착 스트립을 도포한 후 혈장 흡수를 위한 부직포 원단이 뒤따른다. 그리고 요구된 형상이 캐리어 테이프에 펀칭된다. 그런 다음 작은 접착 점들을 붙여 혈장이 빠져나가지 않도록 밀봉한다. 마지막으로 카드를 접착 테이프로 적층하여 밑면을 형성하고 캐리어 층에 접착한다. 그 두 층이 함께 첫 번째 중간 제품을 형성한다. 두 번째 중간 제품인 플라즈마 분리 카드 상부도 이와 비슷한 방식으로 생산된다. 이를 위해 원하는 기하학적 구조로 펀칭하고 후속 단계에서 쉽게 제거할 수 있도록 카드 모서리를 둥글게 만든다. 몇 번의 광학 테스트 단계 후, 두 중간 제품을 접합한 다음 조립 및 라벨 배치를 최종 점검한다.
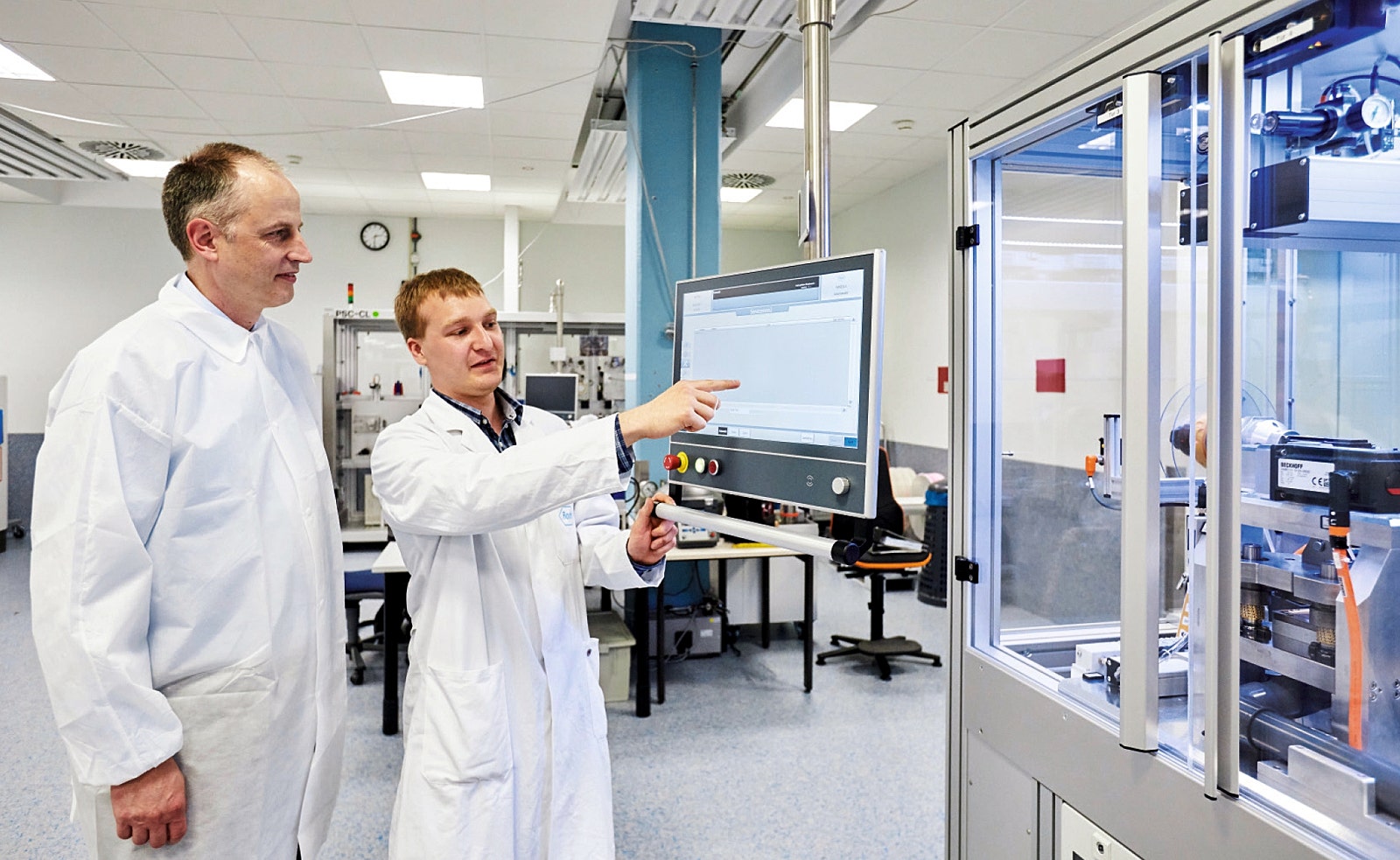
Roche의 전문 엔지니어 Lukas Nagel(오른쪽)은 21.5인치 디스플레이가 있는 CP3221 멀티 터치 패널 PC를 통해 만하임 Beckhoff 영업소의 시스템 컨설팅/영업 부서 소속 Udo Gruber에게 편리한 기계 작동을 보여준다.
민감한 부직포 재료의 정교한 처리
Lukas Nagel은 혈장 분리막의 특수 원단이 매우 민감하고 비용이 많이 든다는 사실을 생산단위의 개발과정에서 고려해야 한다고 말한다. 이로 인해 부직포 절단 시 엄격한 요구사항이 발생한다. 폐기물 발생 비용을 최소화하기 위해서 원하는 기하학적 구조가 요구되어진다. 또한 부직포 원단에 작용하는 힘은 구조물을 변경하지 않아야 하며, 구조물의 투과성을 유지하기 위해 7N을 초과하지 않아야 한다.
이를 보장하기 위해 레이저로 막을 아주 부드럽게 잘라내고, Lukas Nagel의 다음 설명대로 생산 단위에서 특별한 측정 절차가 일어난다. 생산 단위가 시작되면 막이 수집되는 처리 테이블이 측정된다. 그런 다음 시스템은 10개의 모든 XTS 무버에서 인공 구조물 캐리어를 점검한다. 이렇게 하면 모든 구성요소의 공차를 최소화할 수 있다. 가능한 한 적은 공정의 힘을 발휘하기 위해, 막은 진공 그립으로 접착 층에 도포된다. 이처럼 까다로운 제품 처리 환경에서 XTS는 결정된 구성품 공차를 소프트웨어에 쉽게 저장할 수 있다. 따라서 XTS는 전체 생산 공정에 대해 각 무버에 개별적으로 작업을 할당할 수 있다는 큰 이점을 제공한다. 기존 이송 시스템에서 이것은 각 워크 스테이션에서 기계적으로 구현해야 했기에 훨씬 더 복잡했다. 게다가 XTS는 자동으로 추적 기능을 제공한다. 만약 제공되지 않았다면 QR코드를 사용하여 구현해야 했다. 또한 이런 종류의 제품 취급은 효율적인 생산을 용이하게 한다. 왜냐하면 이는 부직포 원단의 어떠한 변형도 공정 초기에 광학적으로 검출될 수 없고, 최종 제품에서만 검출되어 불합격 처리되기 때문이다.
Lukas Nagel은 EL7211 서보 모터 터미널과 AX5000 서보 드라이브를 사용하여 구현된 커팅 유닛, 로터리 테이블 및 트랜스퍼 암과 같은 워크 스테이션에서 모션 축의 정밀도와 소프트웨어 기능의 이점을 높이 평가한다. 하나의 좋은 예시로는, 이벤트에 따라 시간 오프셋 없이 컨트롤러의 실제 위치를 저장하는데 사용할 수 있는 AX5000 서보 드라이브의 측정 프로브 기능이다. 이 기능은 기하학적 구조를 캐리어 테이프에 펀칭 할 때 작동되며, 개발 과정에서 큰 장점이 되었다. 초기에, 정확한 카드 크기나 혈장의 후속 어플리케이션을 위해 펀칭되는 개구의 수는 알려지지 않았다. 리프팅 및 펀칭 순서는 소프트웨어로 필요에 따라 매우 쉽게 조정할 수 있다. 예를 들어, 소프트웨어로 카드 크기는 매우 효율적으로 최적화될 수 있으며, 정의된 어플리케이션 분야 수와 카드 모서리는 반올림될 수 있다.
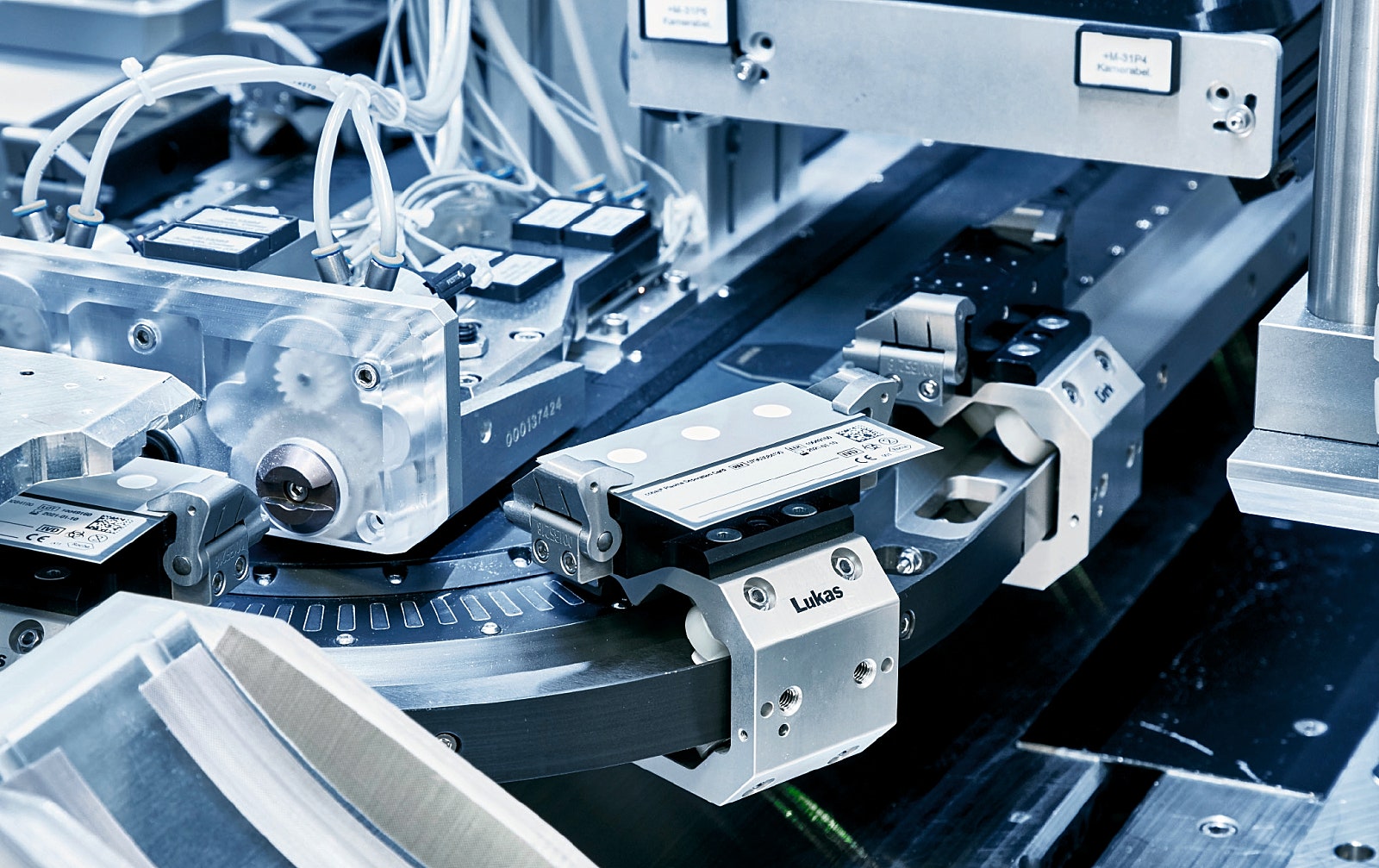
플라즈마 분리 카드 층는 진공 그리퍼를 사용하여 XTS 무버의 공작물 캐리어에 배치되고 생산 및 테스트 스테이션으로 동적 이송된다.
콤팩트한 기계 설계를 위한 XTS
Lukas Nagel은 XTS는 공간을 작게 차지하며 매우 유연하게 제품 이송이 가능하다고 설명했다. XTS를 사용하여 매우 콤팩트한 시스템을 설계할 수 있었고, 이를 제한된 생산환경에서 사용할 수 있게 되었다. 개별 워크 스테이션이 설치되어 있으며, 10개의 무버와 3m 길이의 트랙으로 구성된 XTS가 사용되었다. 첫 번째 예비 제품인 캐리어 층이 한쪽에서 처리되고, 두 번째 예비 제품인 상부 층이 처리된다. 그리고 다른 한 쪽에서는 광학으로 검사된다. 기계 배치는 대칭으로 되어 있다. 장치 중앙에서 막이 잘려 있어 한 번의 XTS 사이클로 완전한 카드를 생산할 수 있다. 처음에 고려되었던 로터리 인덱싱 테이블 기반의 시스템은 규모가 훨씬 더 컷을 것이다.
XTS는 느린 프로세스 시퀀스를 가진 고속 워크 스테이션의 쉬운 동기화 및 동적 사이클을 통해 추가적인 이점을 제공한다. 시간이 많이 걸리는 작업 프로세스를 중복하여 워크 스테이션을 보다 효과적으로 활용할 수 있다. Lukas Nagel은 다음과 같이 말한다. 라인에서 가장 느린 공정은 부직포 원단과 픽앤플레이스의 레이저 커팅 부분이다. XTS를 사용하면 한 번에 6 장의 카드를 준비하고 레이저 커팅 단계로 옮긴 후 해당하는 카드 상단에 개별적으로 붙일 수 있다. XTS가 제공하는 이러한 높은 유연성이 없었다면, 우리는 훨씬 더 큰 막 조각을 가공하거나 여러 개의 이송 스테이션에 대한 공급을 늘려야 했을 것이다. XTS는 가장 느린 공정 단계로 자동 조정되며 각 무버의 현재 처리 상태와 누락된 입력 자료를 기억한다. 그런 다음 무버는 해당 스테이션으로 이동한다. 또한 XTS를 통한 매우 유연한 제품 이송은 결함이 있는 하위 구성요소의 조기배출을 단순화한다. 부품이 불량품으로 인식되는 경우, 무버는 다른 모든 워크 스테이션을 무시하고 부품이 배출될 때까지 다른 무버를 '푸셔(pusher)'로 따른다. 회전식 인덱싱 테이블과 비교하면 XTS는 비생산적인 사이클과 불필요한 추가 거부 처리를 방지해준다.
Roche는 TwinCAT3 XTS 확장 소프트웨어가 제공하는 충돌방지 및 동기화 기능 외에도 Lukas Nagel의 다음 설명처럼 컨트롤러 전류를 제한하는 옵션 혜택을 누릴 수 있다. 우리는 고정 클램프를 열기 위한 인공구조물 캐리어가 기계적으로 고정된 경우에 이 기능을 사용한다. 컨트롤러 전류를 제한하면, 시스템의 다른 곳에서 XTS 엔코더 시스템을 통해 위치 제어를 잃지 않으면서 이 기계의 표준을 단순화한다. 이와 같은 내용의 개념의 기반이 되는 EtherCAT 통신 시스템은 고성능, 간단한 커미셔닝 및 글로벌 표준으로서의 광범위한 사용을 통해 추가적인 이점을 제공한다. Lukas Nagel에 따르면 현장에 탑재된 폼 팩터에서 전력과 통신을 결합한 IP67 등급의 EtherCAT P I/O 모듈도 배선작업을 줄여 생산단위를 단순화하는데 기여한다고 설명한다.
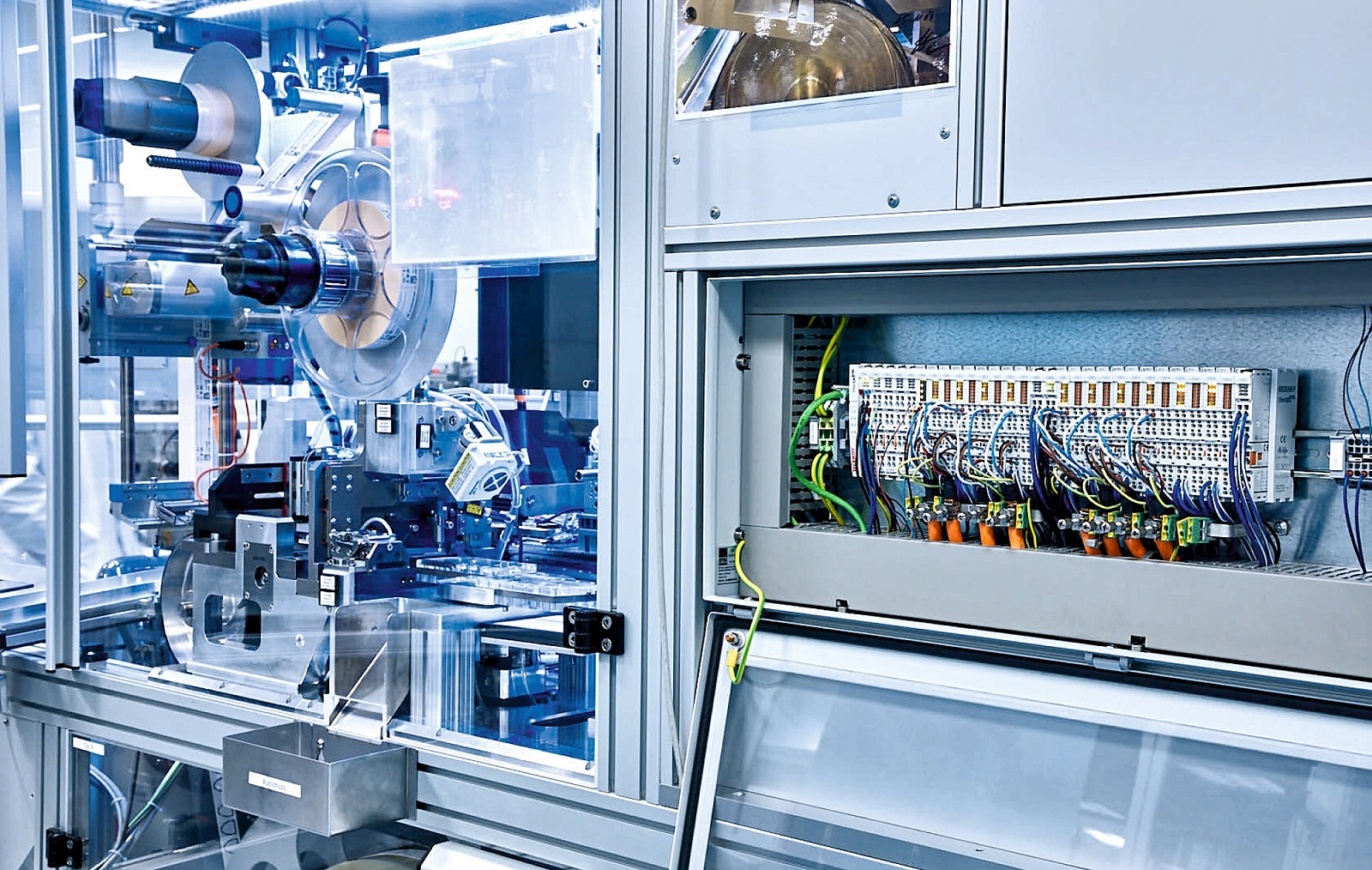
EL7211 서보 모터 터미널(오른쪽)은 여러 축을 포함하는 정확한 모션 시퀀스를 콤팩트하게 보장한다.
At a glance (살펴보기)
제약 산업을 위한 솔루션
- 플라즈마 분리 카드의 생산 단위
소비자 이점
- 출시기간이 짧은 개발 생산 단위
- 콤팩트한 기계 디자인
- 높은 생산 능력을 가진 비용 효율적인 제품 제조
- 기계적 구성요소 대신 XTS 소프트웨어 기능을 통한 유연한 제품 처리
적용된 PC 제어
- TwinCAT 3 XTS 확장 프로그램
- 무버 10개 및 3m 트랙 길이의 XTS
- EL7211 및 AX5000 서보 드라이브
[출처] FA VISION 9월호
[원본] https://www.beckhoff.com/media/downloads/press/2020/korean/2020.09_fa_vision_pcc_0419_roche_k.pdf
댓글
댓글 쓰기